When it comes to industrial machinery such as drills, dies and cutting tools, tool steel is the favored choice. As you can tell by the name, it’s designed for this very purpose. High amounts of carbon and other alloying elements gives tool steel enhanced hardness and strength, qualities which allow it to weather the repeated stresses of manufacturing. But while all tool steel is tough, selecting the right grade of tool steel is important to ensuring you have the type best suited for the job. A good starting point is to first determine the exact purpose of the tool steel you plan to use:
1. Will it be doing work at low temperatures?
2. Will be doing work at high temperatures?
3. Do you intend to use it at high speeds?
4. Will the tool steel be involved in repeated impacts?
5. Will it be used for plastic molding?
6. What is your budget?
Low Temperature Work
For work performed at very low temperatures, the tool steel group known as cold work steel best fits the bill. All tool steels are very hard, but extreme hardness tends to be accompanied by increased risk of cracking. With extreme cold, metal can become even more brittle. So cold work steels are carefully quenched, using methods that allow the steel to retain some degree of flexibility. Quenching in oil (O-series), air (A-series), or adjusting the chemical composition to include more chromium (D-series) produces cold work steel that can perform well in low temperatures. While these cold work steels are pricier than water-hardened types, the mechanical benefits justify the higher cost.
High Temperature Work
Whatever the type of steel, any prolonged exposure to high temperatures will begin to affect its mechanical properties. As the temperature climbs, the atoms in the steel will increase their movement, creating structural changes within the metal. Because tools steels are already heat-treated prior to use, the application of more heat makes them even more vulnerable to structural changes. At worst, it can affect the steel’s crystal structure to the point of reversing the initial heat treatment. To avoid this, hot work steels are formulated with lower carbon and higher alloying content. The increased amount of molybdenum and tungsten produces a steel that can retain its hardness and wear resistance at extreme high temperatures.
High Speed Work
Tool steel used at high speeds are put under a great deal of pressure. High speed tool usage leads to increased friction, which means the steel will be exposed to both heavy wear and high temperatures. This means a metal must possess the durability of hot work steel, and even more resiliency to hold up to the friction. High speed tool steels typically include tungsten, chromium, and vanadium as their alloying elements to produce a very hard steel. This protects it against the pressure and abrasion of high speed work, while its hardness allows it to retain a sharp cutting edge during use.
High Impact Work
To undergo repeated major impacts, the necessary grade of tool steel must have a high degree of shock resistance. Tool steel is prized for its hardness, but that hardness means the metal can crack, chip, or lose its shape with impact. Shock resistant tool steels generally have a lower carbon content along with alloys such as silicon, sacrificing some hardness to give it more ductility and tensile strength. However, this does come at the cost of lower wear resistance. This means high impact tool steels are best suited for impacts only, rather than machinery that will experience more friction and wear.
Plastic Molding Work
The tool steels used for plastic molding are known as the P-series, or special purpose steels. These are much softer than the other types of tool steel due to alloying elements such as nickel, which impedes hardening during the forging process. While the hardness is decreased, P-series tool steel possesses enough malleability to allow it to be shaped into a variety of molding dies. After being heat treated, the tool steel molds can be used to produce plastic items. Theis grade of tool steels are rarely used for any other purpose, because the lengthy and complex manufacturing process makes it more costly to produce.
Cost of Tool Steel
As you can see, the more specialized the task of a tool steel, the more you should prepare yourself to spend. The price tag is well worth it: purchasing the right type of tool steel means it will perform better for its intended work and will last longer while doing it. Choosing the wrong type of tool steel can result in more frequent repairs or even replacements, both requiring an additional cost. However, for general usage not involving any extreme conditions, W-series tool steel will perform well. Due to being water quenched, these steels are the least expensive of all tool steels to produce or purchase. Hand tools, springs, and other small steel goods are typically made of this grade of tool steel.
Category: Tool Steel
Ten Differences between Aluminum and Steel
At first glance, aluminum and stainless steel may appear similar: both a silvery gray, softly shiny, and used to make many of the same products. Many food service and kitchenware items, for instance, are made available from a manufacturer in both types of metals. What separates these two, other than price?
1. Thermal Conductivity
Aluminum is a metal with a high degree of thermal conductivity. What that means in real terms is that a water will boil more quickly in a stockpot than one made of stainless steel. However, aluminum also cools more quickly than stainless, so stainless will help keep a pot of soup warm longer.
2. Thermal Properties
Its lower degree of thermal conductivity means stainless steel is much more resilient to use in high temperatures. Aluminum will begin to soften around 400 degrees Fahrenheit; meanwhile, stainless steel can function well at temperatures up to 800 degrees. Some stainless steel grades can withstand temperatures nearly double that for short periods of work, up to 1500 degrees.
3. Strength
Both metals are quite strong and durable, but stainless steel more so than aluminum.
4. Strength to Weight Ratio
Stainless steel is very strong, but at the cost of a heavier weight. While aluminum is not as strong, manufacturing with this metal will result in an item nearly one third the weight of a steel part. This incredible strength to weight ratio makes aluminum very attractive to manufacturers, especially in the aerospace industry.
5. Welding
Most grades of stainless steel are relatively simple to weld, while aluminum’s high thermal conductivity makes it a more difficult task. However, both are among the most popular types of metals used in welding.
6. Electrical Conductivity
Aluminum has the distinct advantage over stainless steel here, with it being an excellent conductor of electricity. Stainless steel does not conduct electricity well in comparison to other metals.
7. Workability
Pure aluminum is a very soft and malleable metal, and even after alloying, it is easy to cut and form. Due to its strength and hardness, stainless steel takes effort to form into shape.
8. Corrosion Resistance
Both metals are known for excellent corrosion resistance. Chromium is one of the principal alloying agents in stainless steel, and boosts the corrosion resistance of the steel alloy. Aluminum is naturally resistant to corrosion on its own, although it is more vulnerable to damage from highly basic or acidic exposure.
9. Cost
In general, a part made of aluminum will be more affordable than the same item made of stainless steel.
10. Reaction to Foods
Consumers have the choice between aluminum and stainless steel cookware, and often make the decision to purchase aluminum based on price. However, aluminum is a more reactive compound than stainless steel. Acidic foods such as tomato sauces can leave aluminum damaged or with unsightly marks, while other foods like eggs can discolor if cooked or stored in aluminum. While both metals produce high-quality items, choosing stainless steel may be worth some additional money for non-reactive cookware.
What is Tool Steel?
As you might guess, tool steel earns its name by being primarily used for tools. If you then picture a steel screwdriver, pliers, or a wrench, you’d be right – but the items created of tool steel group consist of much more. Within the steel industry, tool steel also refers to machine tools, including those used to manufacture other metal products. To meet the standards of this demanding usage, tool steel is known for being extremely hard, resistant to abrasion and deformation, and its ability to hold a cutting edge. While the steel’s chemical composition is important, the method of production must be carefully controlled to achieve the proper qualities expected in tool steel.
Tool Steel Groups
Tool steel is classed into six groups, all made of carbon steel alloyed with one or more of these main elements: molybdenum, tungsten, chromium, and vanadium. Most tool steel originates from recycled steel scrap, but not all steel scrap is suitable for tool steel. Alloy scrap containing elements which resist oxidation (such as nickel, cobalt or copper) will impede the development of carbides in the metal’s structure, and carbides are crucial to creating tool steel. To ensure the metal will be an optimal mix, tool steel will typically consist of 75% mill scrap supplemented by purchased steel scrap.
The first step is primary melting, where the scrap is heated until molten. Most often this is done in an electric arc furnace (EAF) due to it being a lower-cost production method. However, it is key to avoid contamination during the melting process to create the highest-quality steel. While the EAF is widely used for tool steel, there is some risk of contamination from dust or traces of oxidation-resistant metals from previous batches. For top notch tool steel, an alternate method known as electroslag refining (ESR) is used to melt the steel. Instead of a furnace, ESR uses electric currents to superheat and slowly melt the metal. While a more expensive process, ESR will produce a more refined type of steel without apparent surface imperfections.
After melting and alloying, the steel is poured into ingot molds and then forged into the desired shapes. This is where the six groups of tool steel are determined by their processing:
• Water hardening: Also known as W-group tool steel, this group’s defining property is being water quenched. Quenching in water does risk warping or cracking steel with its rapid cooling, and results in a relatively brittle metal. For this reason, water-hardened tool steel is not considered appropriate for high-temperature industrial uses; once the temperature nears 300 degrees Fahrenheit, there is noticeable softening of the steel parts. Typical items made of W-group steel include scissors, smaller hand tools, and springs.
• Shock-resisting: S-group tool steel is notable for its toughness and ability to withstand repeated impact. This is achieved by using low carbon steel during its production, since higher carbon content results in a harder but more brittle product. Alloying with silicon, tungsten, and chromium gives additional wear resistance and tensile strength. It’s then quenched in oil, which allows for a gentler cooling than water and helps produce a metal with a high degree of durability. Items made of S-group tool steels include tableware dies, impact hammers for nails guns, and shear blades used in cutting heavy steel plate.
• High speed: This group is mainly used for cutting tools, which requires a very hard and abrasion-resistant type of steel. Tungsten, chromium, and vanadium allow HS steel to withstand very high temperatures, such as the heat friction created while cutting other metals. It also manages to hold a cutting edge with repeated use, allowing for higher speeds while cutting without having to pause to resharpen. HS steel can be found in various cutting tools such as drill bits, saw blades, and milling cutters.
• Hot work: Hot-working (H-group) steels are used to cut and shape materials at very high temperatures. To achieve a steel that can withstand prolonged exposure to intense heat, H-group steels are made of a low carbon steel with a higher percentage of alloying content. This produces a tool steel with a high amount of carbides, giving it good overall toughness and wear resistance. The most common use for hot work steel is to produce other metal items because it can withstand the heat needed to forge and cast other metals. It’s used in machinery such as pressure dies, extrusion, and forging equipment.
• Cold work: This tool steel type is narrowed down further into three groups known as the A series (air-hardened), O series (oil-hardened), and D series (high carbon/chromium). All three are intended to be used to cut or form materials at low temperatures.
1. A-series: As the name suggests, steel in this series is hardened via air. Because of the quenching method and its high chromium content, A-series cold work steel is known for low distortion during heat treatment. This makes it a good fit for machining purposes, and so can be found in dies, forming tools, and gauges.
2. O-series: Oil-quenching avoids the cracking and warping risks brought on by water-quenching, and is used for larger parts which require minimal distortion. It offers good wear resistance and toughness, lending itself to a wide range of applications as a general-use cold work steel. Typical uses of O-series tool steel include stamping dies, bushings (metal parts used to absorb vibration and friction), shear blades, and other cutting tools.
3. D-series: Made of a high-carbon steel with a high alloy percentage of chromium, this can also be categorized as a type of stainless steel. However, unlike typical stainless steel, its corrosion resistance is limited and thus is not used to make consumer products. Instead, D-series tool steel applications include cutters, dies, plastic injection molds, and machining rollers.
• Special purpose: this group includes tool steels with alloying elements such as nickel, which typically resist the formation of carbides. The extra time and effort needed to produce these tool steels makes them too expensive for general purposes, so they are manufactured for specific use. Special purpose tool steel can be found in plastic molding dies, zinc die casting, and drills.
What is a Ferrous Metal?
When classifying metals, focusing on a particular property is most often used as a way to divide them into two groups. Is this metal ductile or non-ductile? Is it magnetic or not?
When it comes to ferrous metals, one basic quality determines the groups: whether the metal contains iron. If iron makes up a large percentage of its composition, the metal is considered to be ferrous. If it contains no iron, or just trace amounts of it, it will be labeled a non-ferrous metal.
Beyond that, it becomes more difficult to apply general labels on the groups and the metals’ properties. While ferrous metals can range from iron itself to stainless steel, the alloying elements greatly affect the metal’s characteristics. For example, most ferrous metals are magnetic. But austenitic stainless steel is not, due to the high levels of nickel added to the steel for alloying. The nickel allows the steel to form in a crystal structure that is mostly austenite – and austenite is not magnetic.
So although it can be difficult to generalize about all ferrous metals as a group, there are some general characteristics that can be made about them. Ferrous metals are very hard and strong, especially in comparison to non-ferrous ones such as tin or copper. They’re vulnerable to rust due to their high percentage of iron, unless given corrosion resistance through alloying elements or protective coatings. And they’re usually (but not always) magnetic, which makes them very useful for motor and electrical applications.
The most common categories of ferrous metals include:
- Carbon steel: there’s certainly no question of this being a ferrous metal, with over 90% of its composition being made up of iron. It is very hard and can keep a sharp edge, making it well-suited for mechanical uses such as drill bits and blades.
- Cast iron: this metal is exceptionally hard due to its high levels of carbon, but the carbon also makes it quite brittle. For this reason, cast iron is now primarily used for smaller machine components or cookware.
- Stainless steel: the most commonly used type of ferrous metals, especially for consumer goods. The addition of chromium is what makes a steel stainless, and gives it good corrosion resistance. And it’s magnetic, which is why you can stick magnetics on your refrigerator.
- Alloy steel: the properties of this group of ferrous metals can vary much more widely than the others, since the alloy is specifically formulated for a particular purpose. So while alloy steels are ferrous, the added elements allows the metal to be tailored for more strength, ductility, hardness or other property.
Decoding Steel by its Numbers
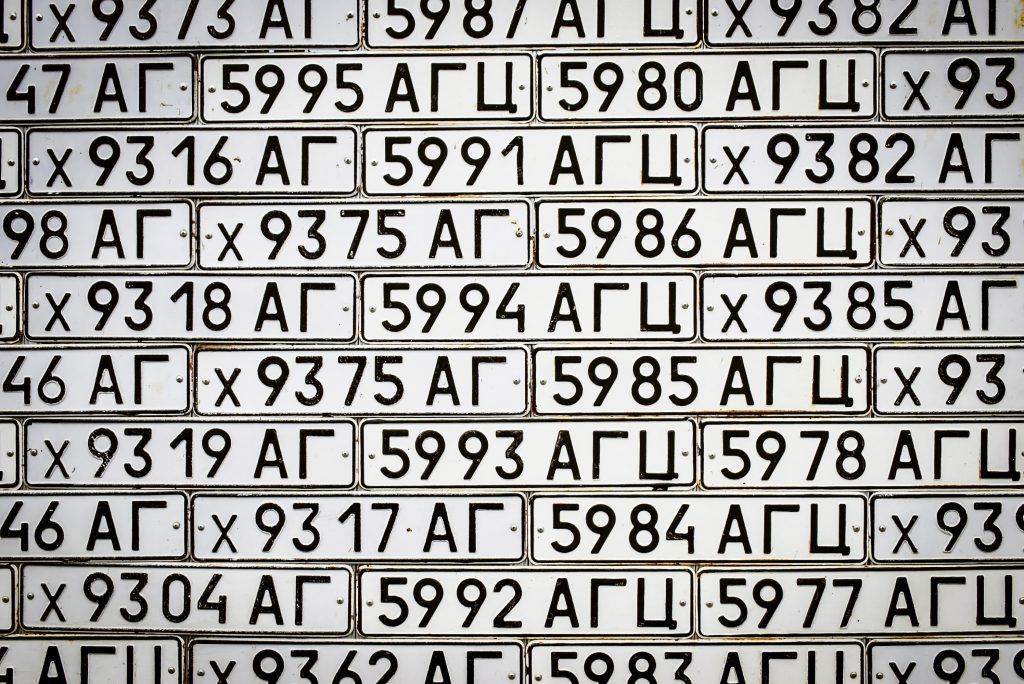
Like any other field of expertise, the steel industry has its own jargon – one that may be confusing upon first encounter. Why are they assigned four-digit codes? What’s the difference between Alloy 4130 and 4140?
Steel is sorted into four main categories as set by the AISI (American Iron and Steel Institute):
- Carbon steel
- Alloy steel
- Stainless steel
- Tool steel
Being steel, these contain the same two basic elements of iron and carbon. Determining their category depends on the percentage of carbon and other alloys added to the iron, which changes the properties of the finished metal.
Within each category, steel can then be classified according to type. This usually includes several of the descriptive factors below:
- Composition: the main categories of carbon, alloy, stainless, and tool steel.
- Microstructure: these are the subcategories of composition. For instance, stainless steel can be classed as ferritic, austenitic, martensitic, and duplex steels.
- Method of production: two methods account for almost all modern steel production, known as EAF (electric air furnace), and BOS (basic oxygen steelmaking).
- Form/Shape: also known as primary forming, creating shapes such as plate or bars.
- Method of finish: this is referred to as secondary forming, the techniques which give the final product its properties and finish. This can include processes such as hot and cold rolling, tempering, or galvanizing.
- Physical strength: using ASTM (American Society for Testing and Materials) standards, the designation typically includes a letter prefix and assigned number.
There are two primary numbering systems used to classify metals, so steel descriptions typically will include both. Along with AISI, the numbering system set by SAE (Society of Automotive Engineers) is most used in the metals industry. For the most part, SAE has adapted their system to align with the classifications set by AISI, so that specifications are standardized for steel.
So with this information, consumers have the ability to recognize the category and classification of a steel item. In the four digit code system, the first number will determine the type:
Starting with 1: Carbon steel
2: Nickel steel
3: Nickel-chromium steel
4: Molybdenum steel
5: Chromium steel
6: Chromium-vanadium steel
7: Tungsten-chromium steel
8: Nickel-chromium-molybdenum steel
9: Silicon-manganese steel and other SAE grades
The following numbers then give additional detail to the specific type of steel. In most cases, the second digit indicates the percentage of alloying element. The last two digits are the percentage of carbon concentration within the steel.
So using the example of 4130 vs 4140 steel: both start with a 4, so they are molybdenum steels – with the concentration of molybdenum being 1%. The difference between the two is that 4130 has a carbon percentage of roughly 0.30%, while 4140 contains 0.40 percent carbon. Because of its lower carbon percentage, 4130 would be more easily machined and weldable than 4140. However, the higher degree of carbon in 4140 alloy gives it greater hardness and strength than 4130. Armed with this knowledge, this may better help you choose the right type of steel for your needs.